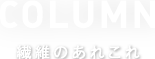
記事を絞り込む
2018.08.09
日本の「繊維産地」1 ~ 東日本編 ~
日本製の高品質な生地・アパレル製品を在庫ストック販売を行う
“生地屋”マスダが日本の誇るべき繊維産地をご紹介いたします!
(当社生地・アパレル製品ラインナップはこちら⇒ 生地・アパレル製品)
繊維は、人間の生活に欠かすことの出来ない三要素「衣・食・住」の一つとして、古くから日本国内で生産され、日本人の生活文化を支えてきました。
そして、繊維製品の輸入比率が異常な高まりを見せる中にあっても、いまだ日本国内には高度な技術の蓄積があります。
当社は、この点に着目し、日本の産地が将来に亘って残っていく事が大切だと考えています。
以下、日本国内の繊維産地の歴史と特徴をご紹介していきます。
↓クリックで拡大します。
【東日本】
①米沢 ②栃尾・見附 ③桐生 ④富士吉田
⑤天龍社 ⑥遠州 ⑦三河 ⑧尾州
【西日本】
⑨北陸 ⑩湖東 ⑪泉州 ⑫丹後
⑬西脇 ⑭三備 ⑮今治 ⑯博多
日本国内の繊維産地の中で、最北に位置しているのが米沢産地です。自然の草木で染めた糸で織り上げられる「米沢織」が有名です。
米沢織の歴史は400年以上前に遡ります。関ヶ原の戦いをきっかけに、会津(現在の福島県)の120万石の大々名であった上杉景勝(うえすぎ かげかつ)が、米沢30万石へ大幅に減封されました。その為、多くの家臣を養う為には、領内の産業発展が最重要課題となり、上杉景勝の重臣であった直江兼続(なおえ かねつぐ)は、従来からの特産品であった青苧(あおそ・麻織物の原料となる)や桑(蚕の食餌)といった、繊維に関わる植物を藩が買い上げることで奨励し、これを製品化して全国へ販売するようになりました。そして江戸後期に、第9代米沢藩主上杉鷹山(ようざん)が、当時の先進地であった新潟の小千谷(おじや)から縮(ちぢみ)の技術を導入し、武士の女性たちに織物生産を習得させ、「米沢織」として強化することによって、困窮する藩の立て直しを目指しました。米沢織は、当初は麻織物でしたが、養蚕が盛んになるにつれ、より高級な絹織物の生産が中心となり、発展を遂げて現代に続いています。
また、明治から昭和にかけ、米沢産地では化学繊維の開発にも取り組まれてきました。大正時代、米沢高等工業学校(現在の山形大学工学部の母体)の講師であった秦逸三(はた いつぞう)が、日本で初めて人工絹糸(レーヨン)を発明しました。同氏はこれをきっかけに帝国人絹株式会社(現在の帝人株式会社)を創設するなど、米沢は、天然繊維と化学繊維の総合産地としての名声を高めました。そうした背景には、絹が天然繊維唯一の長繊維であり、絹織物を模したレーヨン織物を生産するのに適していたことがあると思われます。その証拠に、米沢以外の北陸・富士吉田・桐生といった産地においても、絹織物の産地から化合繊織物の産地へと変遷を遂げていっています。
現代でも「米沢織」は男物の袴用途として、90%以上の全国シェアを誇っており、婦人のスーツやワンピース、フォーマルドレスなどにも用いられ、和装・洋装問わず幅広く愛されています。
共にニット素材で有名で、特にセーターの生産量は男物・女物共に全国1位です。
栃尾産地はニット生地の生産に力を入れており、見附産地はニット製品のOEM生産(※1) がメインです。ニットの産地ではありますが、織物の生産にも長けており、天然繊維から化学繊維、合成繊維までバラエティに富んだ素材を扱う複合型産地です。
※1【OEM生産】
Original Equipment Manufacturing の略で、委託先企業のブランドをつけて販売される商品を、代わりに受注し、生産すること。
実は、もともとの栃尾・見附産地は、江戸時代後期から明治時代初期にかけては、ニットではなく織物の産地で、「栃尾紬(とちおつむぎ)」や「見附結城(みつけゆうき)」といった名産品が有名だったと言われています。
しかし、第二次世界大戦に入ると、軍事需要が最優先され、あらゆる物資が行き渡らなくなりました。これまで産地を支えてきた綿もその例外ではなく、製造・販売が禁止になりました。追い打ちをかけるように企業整備令 (※2) が発動され、転業・廃業が続出し、産地の規模は大幅に縮小されました。こうしたタイミングで織物業者が横編機を導入し創業したことが、ニット産地になった発祥と言われています。
※2【企業整備令】
国家が諸企業を整理・統合し、再編成を指示する法令。1942年公布。
終戦後、1950年代からニット製品ブームが起き、編立機の進化と共に生産量は年々増加していきました。その後も高度経済成長の波に乗り、ニット産地としてのスケールを増していきました。現在は、織物を生産するだけでなく、ニット生地に加えてそれらの製品化まで、関連分野を網羅するトータルファッション産地として存在感を放っています。
桐生産地は、群馬県の東部に位置し、栃木県との県境にあります。絹を用いた「桐生織」で有名です。中でも強撚糸使いの先染めジャガード織物が高く評価されており、使用糸も天然繊維から化合繊まで幅広く対応しています。
桐生で織物が始まった歴史はとても古く、西暦700年の段階で、朝廷に絹を献上した記録が残っています。桑の葉(蚕の餌)の生産に適した土壌だったため、大陸から養蚕の技術が伝来してからは、絹の産地となっていました。
1600年の関ヶ原の戦いに際して、徳川家康より軍旗に使用する絹織物の発注があり、産地にある54ヵ所の村が協力して約2400枚を1日で織り上げたと言われています。徳川軍がこの合戦に勝利をしたことがきっかけで、桐生産地はさらに有名になりました。当時、絹織物の一大産地といえば京都の西陣でしたが、西陣に並ぶ産地となるべく、積極的に技術の導入を試み、大消費都市である江戸に近接している強みも追い風にして、やがては「西の西陣、東の桐生」と呼ばれるまでに成長しました。
明治時代にかけては、力織機(りきしょっき)やジャガード機の導入、マニュファクチュア(工場制手工業制)の確立などにより、さらに発展しました。羽二重(はぶたえ)の創織もこの頃です。和服の裏地などに最適だった羽二重は、美しい風合いが人気で対欧米輸出の中心素材となり、日本の殖産興業を支えました。
こうして帯地・着尺や服飾工芸品などの和装分野で培った桐生の伝統技術は、今では婦人服地・インテリア資材などの洋装分野にも応用されています。また、絹織物だけでなく、化合繊に関するニット・縫製・刺繍・染色整理業などの多様な生産場が点在しているのも桐生産地の特徴的な部分の一つです。
山梨県の東部に位置するこの産地は、先染め・細番手・高密度を特徴とする絹織物が有名で、「郡内織物」と呼ばれています。
富士吉田地方では、約1000年前から織物産地になっていたと言われています。平安時代に施行された法令集「延喜式(えんぎしき)」には、朝廷に生地を貢がせていたという記載がありました。その後、1500年代後半~1600年代、南蛮貿易で渡来した「海気(かいき)」と呼ばれる生地をルーツに絹織物の技術向上がなされ、甲州(甲斐の国)にちなんで「甲斐絹(かいき・かいきぬ)」と呼ばれるようになるほど、富士吉田産地における織物業はさらに発展していきました。
江戸時代、1600年代~1700年代前半は、幕府から奢侈(しゃし)禁止令が発令され、士農工商問わず、着る服の素材や装飾が制限されていました。画一的なファッションを強要された当時の町民たちには不満が募っていました。そんな中で着目されたのが羽織の「裏地」です。表地は素材・色・柄などによる主張を抑え、地味なものにしていましたが、裏地で個性を出すようになりました。その際、先染め・細番手・高密度を特徴としていた「郡内織物」はまさに裏地としては最適な素材で、見事な発色性と繊細な柄を表現できたため、地理的に江戸から離れていたにも関わらず、人気を博していました。
こうして富士吉田産地が長きにわたり発展してきた背景には、富士山の存在なくしては語ることはできません。富士山の麓より流れ出る湧水はきわめて水質が良く、細かな色合いの再現に適しており、織物業を営む上で重宝されてきました。「富士風穴」と呼ばれる、富士山の火山活動による溶岩が流れ込んでできた洞窟も重要です。この空間は、年間平均気温3度前後を維持できる環境になっており、ここで羽化する前の繭を冷凍貯蔵していたのです。このため1年通して養蚕を営むことができるようになりました。家電製品がなかった当時は、この富士山こそが大自然がもたらす冷蔵庫だったと言えます。大正~明治時代にかけて、日本の輸出産業を担う主力製品は絹織物だったため、当時皇太子だった昭和天皇が「富士風穴」を視察された記録も残っています。
第二次世界大戦以降は、絹だけでなく合成繊維やキュプラでの製造も開始されました。現在では、「郡内織物」は洋装の一般化に伴い、ネクタイ、ストール、傘の裏地、インテリア等にも使用されています。今でも、国産ネクタイの4割に使われています。
静岡県東部の天龍社産地は、日本で唯一の別珍(※3)・コーデュロイ(※4)の産地で、国内シェアの95%を占めています。
※3【別珍(べっちん)】
ベルベッティーン、綿ビロードとも呼ばれる綿の緯パイル織物の一つ。
緯糸によってパイルを作り、そのパイルを切断して毛羽を作る。一面に均一な毛羽が出るため、ソフトな肌触りが特徴。
※4【コーデュロイ】
コール天とも呼ばれる綿の緯パイル織物の一つ。
別珍とは異なり、毛羽が縦方向の畝状になっている。厚地で膨らみがあり、保温性が高い。
産地として発達する背景には、1600年代、遠州国磐田郡(現在の磐田市)は、遠州灘に面しており多くの港があったことから、帆船のマスト(帆布)を製織する機屋が存在し、既に織物産業が根付いていたことがあります。その後、1831年に庄屋(しょうや:村役人)の寺田彦左衛門(てらだ ひこざえもん)が、大和地方(現在の奈良)を旅行した際に、目にした雲斎織(うんさいおり・足袋袋などに用いる丈夫な木綿の布)を気に入り、当時の農業・漁業の内職に適しているとしてその技術を取り入れました。このような帆布や雲斎織などの厚地の綿織物を取り扱うノウハウが蓄積されていったことが、天龍社産地でコーデュロイが製造される礎になったといえます。
1890年代、当時の下駄の鼻緒には、輸入品のコーデュロイを使うのが人気でした。それをきっかけに国産化できないかという声が上がり、磐田市では研究を重ねられ、国産のコーデュロイの製織に成功しました。その技術は袋井市・掛川市にも広まり、天龍社産地でコーデュロイの産地が形成されました。その後、別珍製織の研究も進み、1910年頃に完成にこぎつけました。
いずれの用途も、現在ではファッションのみならず資材やインテリアにまで多様化を見せています。生産品種も別珍・コーデュロイだけでなく、一般生地織物や特殊織物の比率も高まってきています。
静岡県西部の遠州産地は、綿織物の産地として有名です。ポプリン、金巾(かなきん)、朱子(しゅす)などの後染め綿織物をメインとしていますが、太番手織物から細番手まで幅広い素材が生産可能です。また、遠州産地は、三河(愛知)、泉州(大阪)と並ぶ、日本三大綿織物産地として知られています。
2017年には「遠州織物」が特許庁の地域団体商標に登録され、地域ブランドとして全国にアピールしていくなど、更なる盛り上がりを見せています。
遠州産地の歴史を紐解いていくと、江戸時代から綿花を栽培しており、綿花の農家は副業として綿織物の生産も併行していました。これが遠州木綿(もめん)と呼ばれていき、高い評価を得ることになりました。
明治時代になると紡績工場がつくられたり、新しい織機を開発したりと、遠州地域の綿織物の生産量は飛躍的に増加し、産地としての地位を確立しました。新織機の開発には、静岡出身の技術者である豊田佐吉(とよだ さきち)や鈴木道雄(すずき みちお)らが携わり、技術革新が進んでいきました。両氏が創業した豊田自動織機製作所、鈴木式織機製作所は、それぞれトヨタ自動車(株)、スズキ(株)の前身となっています。
今の日本の輸出産業を支える有名自動車メーカーの原点は、自動織機製造における鋳造・機械加工技術などを応用したことにより生まれたものだったのです。
「三河木綿(みかわもめん)」「知多晒(ちたさらし)」などの綿織物の白生地産地です。
知多では甚平・手ぬぐい・ガーゼなどの用途で0.5mほどの小巾織物が生産され、蒲郡(がまごおり)では産業・寝装・インテリア用織物やファンシークロスなど柄物が生産されています。このように三河産地は、衣料用テキスタイルだけでなく、日用品・寝装・産業用資材のような、非衣料用繊維製品のウェイトが高いという特徴あります。
三河産地は、日本の綿花栽培発祥の地とされており、799年(延暦18年)に、この地に漂着した崑崙人(こんろんじん:インド人とされる)により、綿の栽培方法が伝来しました。三河地方には、その人物を綿の神様として祭っている天竹神社(てんじくじんじゃ)があります。しかし、残念ながら、この綿花は三河地方の気候・土壌に適応せず、定着しなかったと言われています。
三河地方が綿織物の一大産地として本格的に発展してきたのは、江戸~明治時代です。15世紀の後半に、朝鮮半島から綿布が大量に輸入されるようになり、16世紀には中国(明)からの唐木綿(※5)の輸入が加わって、上流階級では木綿の着用が流行し、綿布の国産化の気運が高まっていきました。
※5【唐木綿】
とうもめん、又はからもめん。外国から輸入された綿布のこと。
上質な木綿として重宝されており、それに劣る国産の綿布は「田舎木綿」と呼ばれて区別されていた。
三河産地で木綿の栽培が始まるのは16世紀初頭ごろで、奈良県興福寺大乗院に残っている「永正年中記」の永正七年(1510年)の年貢に関する記事には、三河木綿の記載があり、当時の奈良でもよく知られていたことが伺えます。 木綿は丈夫で耐久性にすぐれていたため、武士達は袴などの衣料のほか、旗や幕などにも用いられていました。
現代では、産元(産地問屋)を中心に織・染・縫製など一次加工品から最終製品までを地域内で一貫して処理できる産地となりました。三河織物工業協同組合によって、2007年に「三河木綿」が地域団体商標に登録され、更なるブランド力の向上と拡販を目指しています。
尾州産地は国内最大の毛織物の産地で、全国シェアの70%以上を占めています。
イタリアのビエラ、イギリスのハダースフィールドと並ぶ、毛織物の世界三大産地です。
尾州の毛織物は、紳士用スーツ地、コートなどの高級ゾーンに多く用いられています。
産地の最大の特徴としては、糸から織物を作るまでの全工程がこの地域でなされ、分業体制が整っていることです。
企画、織り・編みを行う企業は親機(おやばた)、その協力工場を子機(こばた)と呼び、紡績・染色・補修・整理加工などといった、それぞれの工程を専門で請け負う工場も点在しています。産地内で完結することにより、多品種・少量・短サイクルの生産を可能にしています。
尾州という呼び名は、昔の尾張国の通称からきており、愛知県一宮市、津島市、岐阜県羽島市などがそれに含まれます。元来、尾州産地は、桑(蚕の餌)や綿花の栽培が盛んで、絹織物・綿織物を生産しており、繊維産業を軸に発展してきました。
尾州が毛織物の産地として転換したのは、第一次世界大戦の影響があります。戦争を皮切りに、軍服を作るために毛織物の需要が高まり、ヨーロッパから日本へ毛織物が回ってこなくなってしまいました。自給自足を強いられた日本では、尾州を毛織物の産地とするよう働きかけがありました。理由としては、第一に、この地域がウールの取り扱いに適した湿度を持ち、木曽川の水が染色整理に適していた硬度・鉄分だったため、第二に、国内で初めての毛織機(けおりき)が尾州で開発されたためとされています。
第二次世界大戦後、朝鮮特需の影響もあり、尾州産地はますます毛織物産地としての発展を見せます。余談になりますが、モーニング文化(愛知県を中心とする中京圏内で、コーヒーを頼むとパンやゆで卵などがついてくる午前限定のサービス)は、1950年代の尾州産地において、繊維業を営む人たちが商談の場として喫茶店をよく利用したため、その常連客らの飲み物にゆで卵やピーナッツ菓子のサービスをしたことが発祥といわれています。工場が朝晩絶え間なく稼働し、埃が飛び交っていたため、喫茶店を会社の応接室代わりにしていたようです。当時の尾州産地の繊維業界がとても賑わいを見せていたことがわかります。
日本の「繊維産地」2 ~西日本編~ に続きます。
いかがでしたでしょうか?
ご覧頂き、日本の繊維業界に少しでも興味を持つきっかけとなれば幸いです。
今回ご紹介しきれなかった産地も含め、日本独自の繊維産業は全国津々浦々に広がっています。
マスダ株式会社は、日本全国の産地の近くに支店・営業所を構えネットワーク化し、各産地の新鮮な情報を取り入れつつ、営業活動を行っております。
マスダの「定番」素材に限らず、多くの合成繊維・天然繊維の販売実績があります。
繊維のことならワンストップで対応可能です。お気軽に営業までお問い合わせ下さい。